Research & Development
Innovative capacity through joint work on R&D projects in networks and associations, with renowned universities as well as scientific institutes
Since 1992, the R&D department has been working with numerous companies, universities and research institutes to research new technologies and implement them in manufacturing processes.
We have over 25 years’ experience with topics such as moisture measurement, UV sensors, capacitive measurement technology, glass-ceramic bonding, ceramic gas-tight feedthroughs, additive manufacturing with glass powder and much more.
Glass feedthrough
Research projects
Sensor technology
Glass feedthrough
The Research and Development department supports the glass feedthrough department in the continuous improvement of technology, as well as in the development of new technologies for the production of glass feedthroughs and the individual components required for this. Numerous research projects were carried out, generating further technologies for the processes used in glass feedthrough. These include the insertion of specific materials such as ceramics or titanium, post-processing of the finished glass feedthroughs, such as the application of a bondable gold surface, or alternative fusion technologies.
Research projects
Recently, the Research and Development department has been working intensively on additive manufacturing processes for the production of glass bodies. Binder jetting was the first manufacturing process established in the production processes. At the moment, the R&D department is working on developing, optimising and mastering other additive manufacturing processes such as SLS, FDM as well as SLA processes.
Sensor technology
For more than 20 years, the Research and Development department has been supporting technology development for the production of a wide variety of sensor systems. Alongside numerous attempts to develop a competitive, widely applicable high-precision humidity sensor, other technologies for further sensor systems for ozone detection, gas sensors, microsystem technology, pyrometric hybrid modules, to name just a few, were also developed and partially transferred to production.
Analysis and other services
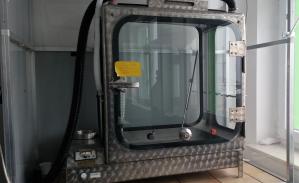
Corrosion testing
For the simulation of industrial atmospheres, i.e. humid air containing sulphur dioxide, the Kesternich test according to DIN EN ISO 6988 and DIN 50018 is used. Due to a rapid corrosion attack on many metals, a lack of corrosion resistance, pores and weak points of protective coatings can be reliably detected.

Roughness measurement
The roughness measuring device WRT-160 (Wolpert, Europe) can be used to measure the roughness of a wide variety of surface structures and to quantitatively record and output almost all roughness parameters. In addition to the feed unit, the unit also has an evaluation unit. An integrated thermal printer enables a quick comparison of several measurements, among other things. The selection of different standards (DIN/ISO/JIS/ASME) enables measurements according to these standards.
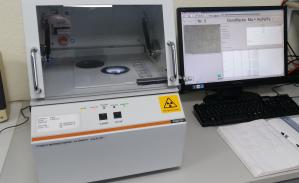
Layer thickness measurement
The coating thickness gauge “FISCHERSCOPE® X-Ray XULM®” is used for highly accurate determination of coating thickness, particularly that of precious metal coatings and coating systems. It is also used for material analysis. In the FISCHERSCOPE® XULM®, the X-ray tube and detector system are positioned below the measuring table. Accordingly, the measuring direction is from bottom to top. This offers particular advantages when measuring small parts with frequently changing geometry such as the smallest housing parts or electrical contact pins.
Contacts